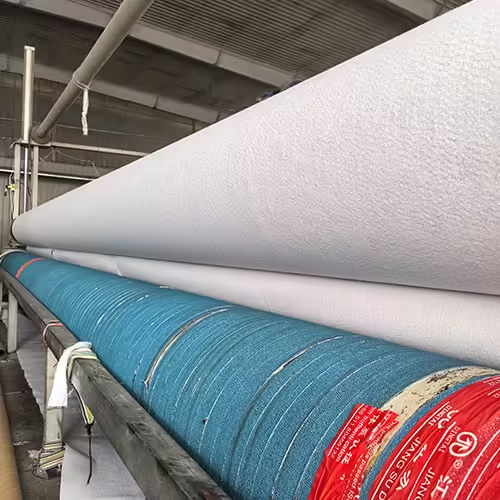
Welcome to My Blog!
Before we dive into the content, I’d love for you to join me on my social media platforms where I share more insights, engage with the community, and post updates. Here’s how you can connect with me:
Facebook:https://www.facebook.com/profile.php?id=61576267991871
Now, let’s get started on our journey together. I hope you find the content here insightful, engaging, and valuable.
Table of Contents
Introduction
In civil engineering, geotextiles are critical to the stability, drainage and long-term success of a project, providing solutions that traditional methods cannot. Understanding how to choose the best geotextile manufacturer is critical.
EcoGeo Material is a geosynthetics factory located in Shandong, China, where we manufacture high-quality geotextile fabric and other materials. We are committed to providing powerful solutions for water conservancy, environmental protection, municipal engineering, and more. This guide will help you understand what makes up a leading geotextile fabric manufacturers and why your choice is critical to the success of your project.
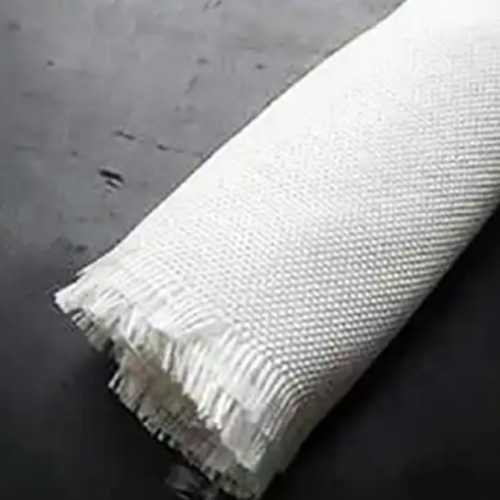
Understanding Geotextile Fabric: An Essential Overview
Before diving into the specifics of manufacturers, it’s crucial to grasp what geotextile fabric is and its diverse functions. Geotextiles are permeable textile materials used in conjunction with soil, rock, or earth in geotechnical engineering applications. They are designed to improve the performance of soil and rock structures, providing capabilities that enhance their stability, durability, and effectiveness.
What is Geotextile Fabric?
Unlike geomembranes, which are impermeable barriers, geotextile fabric allows fluids to pass through while retaining soil particles. This unique characteristic enables them to perform several vital functions within various construction and environmental projects. They are typically made from synthetic polymers such as polypropylene or polyester, which are resistant to biodegradation, chemicals, and UV degradation, ensuring long-term performance in demanding environments.
Key Functions of Geotextile Fabric
Geotextile fabric serves multiple purposes, often simultaneously, within a single application:
- Separation: Prevents the intermixing of dissimilar materials (e.g., aggregate and subgrade soil), maintaining the integrity and function of each layer. This is vital in road construction to prevent the contamination of base courses.
- Filtration: Allows water to pass through while retaining fine soil particles, preventing clogging and ensuring efficient drainage. This is critical in drainage systems, retaining walls, and erosion control.
- Drainage: Provides a pathway for water flow, effectively collecting and conveying liquids or gases within the plane of the geotextile. This accelerates consolidation and reduces pore water pressure.
- Reinforcement: Imparts tensile strength to soil, increasing its load-bearing capacity and stability. This is particularly useful in retaining walls, steep slopes, and embankments.
- Protection: Acts as a cushion or barrier to prevent damage to other geotechnical materials, such as geomembranes, from punctures or abrasion caused by sharp aggregates.
Why Choosing the Right Geotextile Fabric Manufacturers Matters
The performance of geotextile fabric directly impacts the success and longevity of your project. Substandard materials or inconsistent quality can lead to project failures, costly repairs, and significant environmental repercussions. This is why selecting the right geotextile fabric manufacturers is a decision that requires careful consideration.
A reliable manufacturer ensures:
- Consistent Quality: High-quality raw materials and stringent manufacturing processes lead to products that meet specified performance criteria without variation.
- Technical Expertise: Reputable manufacturers offer technical support, helping engineers select the most appropriate geotextile fabric for specific project challenges.
- Compliance with Standards: Products meet national and international industry standards, ensuring safety, reliability, and regulatory compliance.
- Innovation: Leading manufacturers invest in R&D, providing advanced solutions that improve efficiency and performance.
- Reliable Supply Chain: Consistent product availability and timely delivery are crucial for project timelines.
What to Look for in Best Geotextile Fabric Manufacturers
Identifying the best geotextile fabric manufacturers involves evaluating several key factors that speak to their capability, reliability, and commitment to quality.
1. Product Range and Versatility
A top manufacturer should offer a comprehensive range of geotextile fabric types to meet diverse project needs.
- Woven Geotextiles: Known for their high tensile strength and low elongation, ideal for separation and reinforcement applications.
- Nonwoven Geotextiles: Characterized by their excellent filtration, drainage, and protection properties, often used for cushioning and separation.
- Knitted Geotextiles: Less common but offer specific benefits for certain applications requiring flexibility.
The ability to provide customized solutions based on unique project specifications also indicates a manufacturer’s expertise.
2. Quality Control and Certifications
Quality assurance is paramount. Look for geotextile fabric manufacturers with robust quality control systems in place, from raw material inspection to final product testing.
- ISO Certifications: Indicates adherence to international quality management standards.
- ASTM/GRI Standards: Compliance with relevant industry testing standards (e.g., ASTM D4437 for general test methods, GRI GM13 for nonwoven geotextiles) ensures products perform as expected.
- Third-Party Verification: Independent testing and certification provide an unbiased assessment of product quality.
3. Manufacturing Capabilities and Technology
The sophistication of a manufacturer’s production facilities directly impacts product quality and consistency.
- Advanced Equipment: Modern machinery ensures precise control over manufacturing processes, leading to superior geotextile fabric.
- Production Capacity: Sufficient capacity to meet large project demands without compromising quality or delivery schedules.
- Sustainable Practices: Manufacturers committed to environmentally friendly production processes are increasingly preferred.
4. Technical Support and Expertise
Beyond just selling products, the best geotextile fabric manufacturers provide invaluable technical support.
- Engineering Assistance: Helping clients select the right geotextile fabric, design appropriate layouts, and understand installation procedures.
- On-Site Support: For complex projects, the availability of on-site technical assistance can be a significant advantage.
- Research and Development: A commitment to innovation ensures the continuous improvement of products and the development of new solutions.
5. Reputation and Track Record
A manufacturer’s history and reputation within the industry speak volumes.
- Client Testimonials and Case Studies: Review successful past projects and client feedback.
- Industry Recognition: Awards, memberships in professional associations, and peer recognition can indicate a manufacturer’s standing.
- Years in Business: While not the sole indicator, a longer history often suggests stability and experience.
Leading Geotextile Fabric Applications by Function
Geotextile fabric is not a one-size-fits-all solution; its application depends heavily on its specific function and the project’s demands. Understanding these applications helps in appreciating the diverse capabilities that reliable geotextile fabric manufacturers must offer.
Primary Function | Common Applications | Benefits of Using Geotextile Fabric |
Separation | Roadways, railways, aggregate base courses, unpaved roads | Prevents mixing of dissimilar soil layers, extends pavement life, reduces aggregate consumption |
Filtration | Subsurface drainage systems, retaining walls, erosion control structures, landfill leachate collection | Prevents clogging of drainage media, maintains hydraulic efficiency, reduces maintenance |
Drainage | Landfill gas collection, road/railway drainage, sports fields, mining heap leach pads | Accelerates consolidation, reduces pore water pressure, improves stability, enhances water removal |
Reinforcement | Retaining walls, steepened slopes, embankments over soft soils, basal reinforcement | Increases soil stability, improves load-bearing capacity, reduces required fill volume, allows steeper slopes |
Protection | Geomembrane protection layers in landfills and ponds, pipeline padding | Prevents puncture and abrasion damage to critical liners, extends system lifespan |
Erosion Control | Riverbanks, coastal protection, vegetated slopes, ditch lining | Stabilizes soil, prevents washout, promotes vegetation growth, reduces sediment runoff |
Containment | Waste containment facilities (landfills), hazardous waste storage, secondary containment | Forms part of composite lining systems to prevent leakage, ensures environmental safety |
The Manufacturing Process: From Polymer to Project Solution
Understanding the general manufacturing process behind geotextile fabric provides insight into the quality control points and the technical expertise required from geotextile fabric manufacturers.
1. Raw Material Sourcing
The process begins with sourcing high-quality synthetic polymers, primarily polypropylene (PP) or polyester (PET), in pellet form. The purity and consistency of these raw materials are critical to the final product’s performance.
2. Extrusion
The polymer pellets are melted and then extruded into continuous filaments or slit films. This step determines the basic form of the fibers that will make up the geotextile fabric.
3. Fabric Formation
- For Woven Geotextiles: The extruded filaments are woven together on industrial looms, similar to traditional textile weaving, creating a strong, stable fabric with distinct tensile properties.
- For Nonwoven Geotextiles: The filaments are randomly laid down to form a web, which is then bonded together. Bonding methods include needle punching (mechanical entanglement), thermal bonding (heat), or chemical bonding. Needle punching is common for heavy-duty nonwovens due to its robust interlock.
4. Finishing and Treatment
After formation, the geotextile fabric may undergo various finishing treatments to enhance specific properties. This can include:
- Heat Setting: To improve dimensional stability and strength.
- UV Stabilization: Adding additives to resist degradation from ultraviolet radiation, critical for long-term outdoor exposure.
- Calendering: Passing the fabric through heated rollers to control thickness and surface properties.
5. Quality Assurance and Testing
Throughout the entire process, rigorous quality control checks are performed. Samples from each batch are subjected to a battery of tests to ensure they meet required specifications. These tests can include:
- Tensile Strength: Measuring the force required to break the fabric.
- Puncture Resistance: Assessing the fabric’s ability to resist penetration.
- Permittivity/Flow Rate: Determining how quickly water passes through the fabric.
- Apparent Opening Size (AOS): Measuring the pore size distribution.
- UV Resistance: Testing durability under simulated sunlight.
6. Rolling and Packaging
Finally, the finished geotextile fabric is rolled onto large cores and packaged for shipping. Proper packaging protects the material from environmental damage during transport and storage.
Case Studies and Real-World Impact
The tangible benefits of selecting reputable geotextile fabric manufacturers are best illustrated through real-world applications. Across the globe, geotextiles are foundational to critical infrastructure.
- Road Construction in Challenging Terrain: In regions with soft or unstable subgrades, geotextile fabric is used for separation and reinforcement, distributing loads more evenly and preventing aggregate from sinking into the subgrade. This significantly extends the life of roadways and reduces maintenance.
- Landfill Design: Nonwoven geotextiles protect geomembranes from puncture by sharp aggregate, while woven geotextiles are used for separation layers in leachate collection systems, ensuring the long-term integrity of waste containment facilities.
- Coastal Erosion Protection: Geotextile bags filled with sand are an environmentally friendly alternative to traditional rock revetments, providing flexible and effective erosion control along coastlines and riverbanks.
- Sports Field Drainage: Geotextile fabric layers are crucial beneath modern sports fields, facilitating rapid drainage after rain and maintaining a consistent playing surface.
These examples underscore that the choice of geotextile fabric manufacturers directly influences the safety, longevity, and environmental performance of these essential projects.
EcoGeo Material: Your Partner in Geotextile Solutions
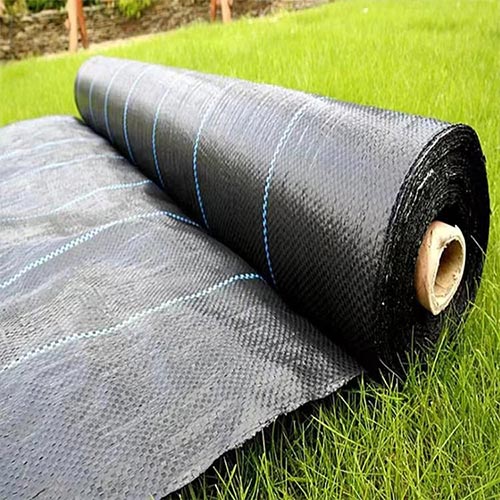
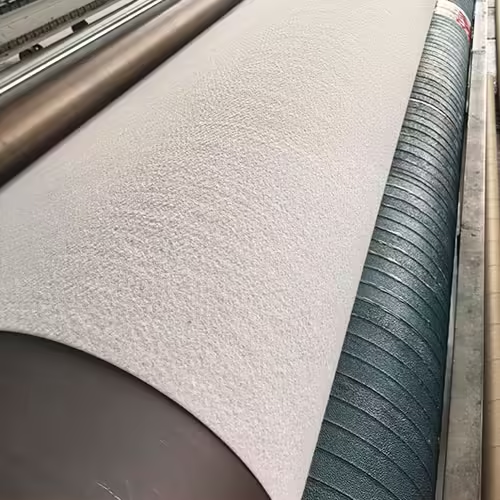
At EcoGeo Material, we understand that finding the right geotextile fabric manufacturers is crucial for your project’s success. Located in Shandong Province, China, our state-of-the-art facility is equipped with advanced production lines dedicated to manufacturing a wide range of high-quality geotextiles. We adhere to stringent quality control protocols, ensuring every roll of geotextile fabric meets international standards for performance, durability, and reliability.
Our expertise extends beyond manufacturing. We are committed to being a comprehensive partner for our clients, offering:
- Diverse Product Portfolio: From high-strength woven geotextiles for reinforcement to highly permeable nonwoven geotextiles for filtration and drainage, we offer solutions for every application.
- Technical Support: Our experienced engineering team provides expert advice, helping you select the optimal geotextile fabric for your specific project challenges and assisting with design considerations.
- Customization Capabilities: We can tailor geotextile fabric specifications to meet unique project requirements, ensuring a perfect fit for your needs.
- Reliable Supply Chain: Our efficient logistics ensure timely delivery, keeping your project on schedule and within budget.
Our products are widely applied in critical sectors such as water conservancy, environmental protection (including waste treatment and landfill lining), municipal engineering, aquaculture, and mining restoration. Whether your project involves stabilizing a new road, designing an efficient drainage system, or protecting valuable geomembranes, EcoGeo Material has the expertise and the quality geotextile fabric to ensure its success.
Conclusion
The selection of the best geotextile fabric manufacturers is a foundational decision that profoundly impacts the success, safety, and longevity of any civil engineering or environmental project. High-quality geotextile fabric is not merely a component; it is an enabling technology that transforms design possibilities, enhances performance, and delivers long-term value. By prioritizing manufacturers who demonstrate a commitment to quality, technical expertise, innovation, and reliable supply, project stakeholders can mitigate risks, optimize costs, and ensure the robust performance of their infrastructure.
Investing in superior geotextile fabric solutions is an investment in a more resilient and sustainable future. For your next project, choose a partner dedicated to excellence and environmental responsibility. Contact EcoGeo Material today to discuss your project needs and discover how our high-quality geotextile fabric solutions can provide the robust foundation your infrastructure demands.
FAQ
Why is choosing the right geotextile fabric manufacturers so important for my project?
Selecting a reputable geotextile fabric manufacturers ensures you receive high-quality, reliable materials that meet industry standards. This directly impacts your project’s stability, longevity, and overall success, preventing costly failures and environmental issues.
What should I look for in top geotextile fabric manufacturers?
When evaluating geotextile fabric manufacturers, prioritize those with a wide product range, stringent quality control certifications, advanced manufacturing capabilities, excellent technical support, and a strong industry reputation.
How do geotextile fabric manufacturers ensure product quality?
Leading geotextile fabric manufacturers implement rigorous quality control from raw material sourcing to final product testing. They often hold ISO certifications and adhere to international standards like ASTM/GRI for tensile strength, puncture resistance, and permeability.
Can geotextile fabric manufacturers provide solutions for specific applications like erosion control or drainage?
Absolutely. Reputable geotextile fabric manufacturers offer diverse product lines designed for various functions, including separation, filtration, drainage, reinforcement, and protection. They can help you select the ideal geotextile fabric for your specific needs, such as erosion control or subsurface drainage.
What makes EcoGeo Material a reliable geotextile fabric manufacturers?
EcoGeo Material, based in Shandong, China, is a dedicated geotextile fabric manufacturers committed to high-quality research, development, and production. We offer a comprehensive range of geotextiles and other geosynthetics, backed by strong technical support, ensuring robust solutions for water conservancy, environmental protection, municipal engineering, and more.